How Wind Tunnel Testing Enhances Aerodynamic Performance
- randymason1991
- Jan 31
- 8 min read
Wind tunnel testing is one of the most essential tools used in the aerospace, automotive, and other engineering sectors to understand and optimize aerodynamic performance. Through the use of controlled airflows, engineers can simulate real-world conditions and test how different shapes, surfaces, and configurations affect the performance of an object, such as an aircraft, vehicle, or building. In the aerospace industry, the importance of wind tunnel testing cannot be overstated. It plays a critical role in ensuring the safety, efficiency, and overall performance of aircraft, making it an indispensable part of the design and development process.
In this article, we will explore how wind tunnel testing works, its significance in aerodynamic performance, and the ways in which it enhances the design of modern aircraft.
What is Wind Tunnel Testing?
A wind tunnel is a device used to create controlled airflow around a stationary object or a scaled model of an object. This process allows engineers to simulate the effects of airflow on an object in a controlled environment, which is not always possible in real-world conditions. By observing how the object interacts with the air, engineers can gather valuable data about its aerodynamic properties.
Wind tunnels are typically large, enclosed chambers with fans that generate a continuous stream of air. The object being tested, such as a model aircraft or vehicle, is placed in the test section of the tunnel, where sensors and cameras capture various aspects of its performance under different airspeed and flow conditions. These tests can simulate a wide range of real-world scenarios, including takeoff, cruise, and landing for aircraft, or high-speed driving conditions for vehicles.
Wind tunnel testing is valuable because it provides real-time feedback on how the object performs aerodynamically without the risks and costs associated with flight tests or road tests. The data gathered can then be used to optimize the design and performance before physical prototypes are built.
Enhancing Aerodynamic Performance
One of the primary benefits of wind tunnel testing is its ability to enhance aerodynamic performance. Aerodynamics is the study of how air interacts with solid objects, and it plays a crucial role in determining the efficiency, speed, and stability of an aircraft or vehicle. By simulating airflow patterns in a wind tunnel, engineers can observe how different design changes affect the object's performance in the air.
1. Reducing Drag and Improving Fuel Efficiency
Drag is one of the key factors that impact the efficiency of an aircraft or vehicle. It refers to the resistance an object experiences as it moves through the air, and it increases with the object’s speed. In the aerospace industry, reducing drag is critical for improving fuel efficiency and overall performance. Wind tunnel testing allows engineers to test different configurations and aerodynamic shapes to determine how they affect drag.
For example, the shape of an aircraft’s fuselage, wings, and tail can significantly influence the amount of drag it experiences. Through wind tunnel testing, engineers can refine these elements to minimize drag. Streamlining the shape of an aircraft reduces the amount of turbulence and resistance encountered as it moves through the air, leading to better fuel efficiency and improved performance.
Wind tunnel testing also enables engineers to test various surface treatments and materials to see how they affect airflow and drag. For example, certain coatings or surface roughness patterns can help reduce drag by promoting smoother airflow over the aircraft's surface.
2. Optimizing Lift and Stability
In addition to reducing drag, wind tunnel testing is essential for optimizing lift and stability. Lift is the force that allows an aircraft to stay in the air, and it is generated by the interaction between the wings and the air flowing over them. The design of the wings, their shape, size, and the angle at which they meet the airflow are all critical factors that determine how effectively lift is generated.
Through wind tunnel testing, engineers can experiment with different wing configurations to determine the optimal design for lift generation. For example, a larger wing surface can generate more lift, but it can also increase drag. The challenge lies in finding the balance between these two forces to achieve optimal performance.
Wind tunnel testing also helps engineers test the stability of an aircraft by simulating various flight conditions, such as turbulence, high-speed turns, or sudden changes in altitude. This allows them to identify any potential issues with stability and make design adjustments to ensure the aircraft remains balanced and controllable in all conditions.
3. Identifying Flow Separation and Stall Conditions
Flow separation occurs when the smooth airflow over an aircraft’s surface is disrupted, causing turbulence and a loss of lift. This can lead to a stall, where the aircraft loses its ability to fly effectively and can even result in a dangerous loss of control. By using a wind tunnel, engineers can observe flow patterns and identify areas where flow separation might occur.
Wind tunnel testing allows engineers to simulate conditions that could cause flow separation, such as high angles of attack during takeoff or landing. By identifying these conditions early in the design process, engineers can make changes to the shape or angle of the wings or fuselage to prevent flow separation and reduce the risk of stall.
For instance, adding winglets at the tips of the wings can help improve the airflow and reduce the chances of flow separation at high angles of attack. Similarly, modifying the shape of the leading edge of the wings can improve airflow and delay the onset of a stall.
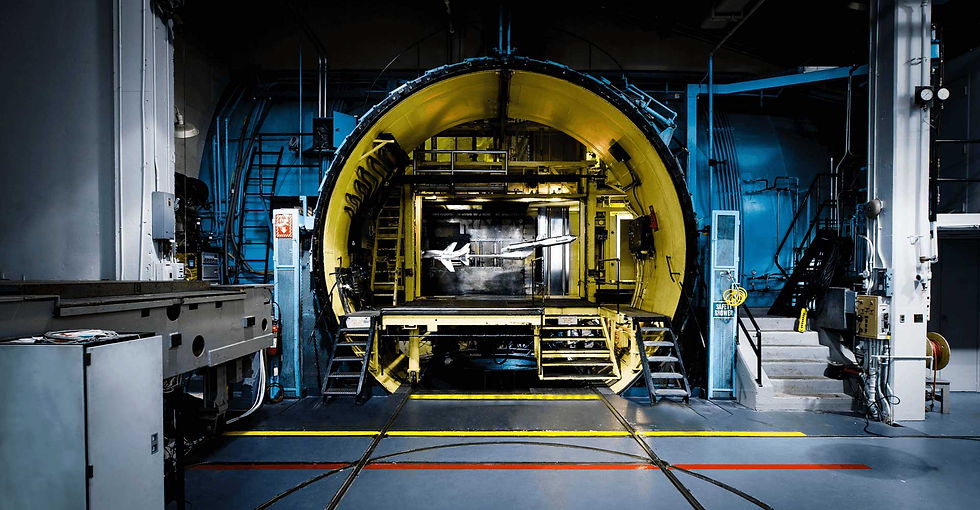
Testing New Aircraft Designs and Innovations
Wind tunnel testing is not only used to optimize existing designs but also plays a critical role in testing new and innovative aircraft concepts. As technology continues to evolve, engineers are constantly exploring new materials, propulsion systems, and aerodynamic concepts to improve aircraft performance.
For example, the development of unmanned aerial vehicles (UAVs) and electric aircraft has introduced new challenges and opportunities in aerodynamic design. Wind tunnel testing is essential for understanding how these new technologies behave in real-world conditions and for refining their designs to ensure they meet performance and safety standards.
Electric aircraft, in particular, pose unique aerodynamic challenges because they typically require different propulsion systems and have different weight distribution compared to traditional aircraft. Wind tunnel testing allows engineers to assess the impact of these new configurations on aerodynamics and make adjustments to optimize performance.
Similarly, wind tunnel testing is essential for testing the effectiveness of new wing designs, such as those with variable geometry or morphing capabilities. These innovations aim to improve the aircraft's performance by adjusting the wing shape during flight, but they require rigorous testing to ensure they function as intended and do not compromise safety or stability.
The Role of Computational Fluid Dynamics (CFD) in Wind Tunnel Testing
While wind tunnel testing is an essential tool for improving aerodynamic performance, it is often used in conjunction with computational fluid dynamics (CFD) simulations. CFD is a type of computer simulation that models the airflow around an object and predicts how it will behave under various conditions. CFD can help engineers identify potential issues and refine designs before conducting wind tunnel tests.
However, while CFD simulations provide valuable insights, they cannot replicate the accuracy and real-world conditions of wind tunnel testing. Wind tunnel testing remains the gold standard for validating CFD models and ensuring that the design performs as expected. By combining the strengths of both CFD and wind tunnel testing, engineers can achieve more precise and efficient designs.
The Limitations of CFD and the Need for Wind Tunnel Validation
While CFD offers immense value in the initial stages of design and optimization, there are several limitations that can impact its accuracy. One of the most significant challenges is the complexity of accurately simulating real-world flow conditions. While CFD can model fluid behavior, the computational power required to solve complex aerodynamics equations becomes significantly higher as the conditions become more dynamic, such as in high-speed or turbulent flows. Moreover, the assumptions made in CFD models—such as uniform air properties or simplified boundary conditions—can introduce errors that affect the reliability of the predictions.
Additionally, CFD models may not fully capture the effects of small-scale features on aerodynamic performance, such as surface roughness, minor imperfections, or variations in material properties. These factors, though seemingly trivial, can significantly affect the behavior of airflow over an object and are often best observed through wind tunnel testing. Wind tunnel testing, therefore, remains invaluable as it allows engineers to capture real-world phenomena that might not be perfectly replicated in computational simulations.
Thus, CFD and wind tunnel testing work in tandem to complement each other. CFD can be used to rapidly iterate through different design concepts and generate initial performance predictions, while wind tunnel testing provides the empirical data required to validate and refine those predictions. By combining both approaches, engineers can optimize their designs with greater confidence, knowing that both theoretical simulations and physical tests support their decisions.
Improving Wind Tunnel Accuracy with CFD
In some cases, CFD and wind tunnel testing are not separate activities but are integrated into a single workflow to enhance the overall accuracy of aerodynamic studies. For instance, CFD simulations are often used to predict the flow patterns and behavior of an object before a physical wind tunnel test. This allows engineers to set up the physical test more effectively, focusing on areas where CFD predictions suggest potential issues. During the wind tunnel test, the data collected can be compared with CFD results to identify discrepancies and refine the models, ensuring a higher degree of precision.
In particular, for complex shapes or unconventional designs, CFD can provide preliminary insights that guide wind tunnel setup and testing procedures. For example, an experimental aircraft with an innovative wing shape may require a unique testing methodology to assess how the airflow behaves at various angles. CFD simulations can predict the airflow behavior in advance, allowing engineers to design specialized testing conditions that replicate those expected in real-world flight scenarios.
This hybrid approach is particularly useful in the aerospace industry, where the cost of testing can be high, and the need for accurate results is critical. CFD can minimize the number of physical tests needed by narrowing down the potential solutions, while wind tunnel testing can confirm the CFD predictions and ensure that the design is both practical and safe. The synergy between these two approaches leads to more efficient, effective aerodynamic optimization.
Future Trends in Wind Tunnel Testing and CFD Integration
As technology continues to advance, the integration of CFD and wind tunnel testing will become even more seamless. The growing power of computational systems and the development of more sophisticated algorithms will allow for more accurate and detailed simulations, reducing the gap between CFD predictions and physical testing outcomes.
Moreover, new innovations in sensor technology and real-time data analysis will enhance the accuracy of wind tunnel testing. For example, advanced pressure sensors and high-speed cameras are now being used in wind tunnels to provide a wealth of data on the behavior of airflow at a much finer level of detail than ever before. These sensors can track minute changes in airflow patterns and help engineers capture the complexities of aerodynamic behavior that may be difficult to identify with earlier methods.
Additionally, advancements in artificial intelligence (AI) and machine learning (ML) could play a significant role in improving both CFD simulations and wind tunnel testing. AI algorithms can analyze large datasets from both CFD and wind tunnel tests to identify patterns and correlations that human engineers might miss, ultimately leading to more precise predictions and faster optimization cycles. As these technologies evolve, they will enable a more holistic and efficient design process, where CFD and wind tunnel testing complement each other even more effectively.
Conclusion
Wind tunnel testing is an indispensable tool in the field of aerospace engineering, offering engineers the ability to simulate and analyze the aerodynamic performance of aircraft under a wide range of conditions. Through the use of wind tunnel testing, engineers can reduce drag, optimize lift, enhance stability, and prevent flow separation, ultimately leading to more efficient and safer aircraft designs.
As the demand for advanced, high-performance aircraft continues to grow, wind tunnel testing will remain a cornerstone of aerodynamic development. Whether testing new innovations like electric propulsion systems or refining traditional aircraft designs, wind tunnel testing plays a critical role in pushing the boundaries of what is possible in aviation. By ensuring that designs are thoroughly tested and optimized before they take to the skies, wind tunnel testing helps to create aircraft that are not only efficient and safe but also capable of meeting the challenges of the future.
Commentaires